Soudronic
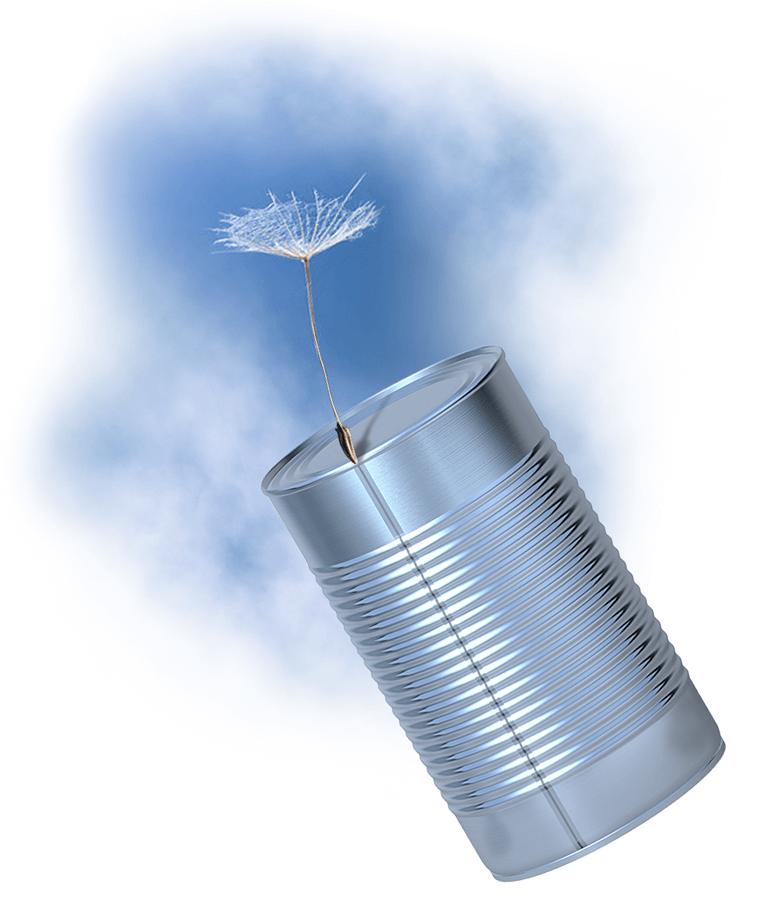
For some years now Soudronic has championed the claim of steel tinplate to be one of the most economical, environment-friendly and sustainable forms of packaging available to manufacturers today. And there is no shortage of reasons. First and foremost is the fact that metal cans today require far less raw material than in the past. Soudronic leads the way in the development of the advanced canmaking machines needed to work with downgauged tinplate, i.e. sheet metal stock of as little as 0.1 mm in thickness. Lighter cans mean more containers per ton of tinplate, savings on natural resources and, overall, a significant reduction in the world’s carbon emissions footprint.
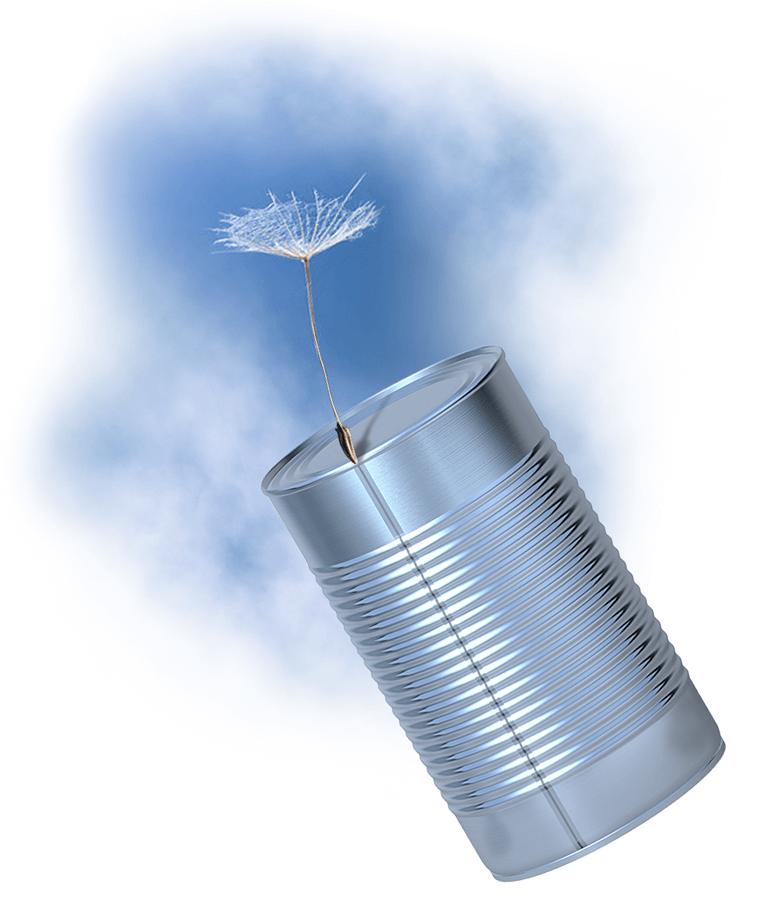
For some years now Soudronic has championed the claim of steel tinplate to be one of the most economical, environment-friendly and sustainable forms of packaging available to manufacturers today. And there is no shortage of reasons. First and foremost is the fact that metal cans today require far less raw material than in the past. Soudronic leads the way in the development of the advanced canmaking machines needed to work with downgauged tinplate, i.e. sheet metal stock of as little as 0.1 mm in thickness. Lighter cans mean more containers per ton of tinplate, savings on natural resources and, overall, a significant reduction in the world’s carbon emissions footprint.
3- Piece CAN Production
We design, construct, install and maintain fully integrated canbody production lines, operating from very low speeds to a maximum of 1200 cans per minute. Typically, a production system has six separate stations: a slitter to cut the tinplate base material into body blanks of the required size; a transfer system to feed the cut blanks from the slitters to the canbody welder; a welding unit to shape and weld the canbody; a seam protection system to prevent oxidation and chemical reactions damaging the welded can; a curing system to dry and harden the seam protection; and a bodyformer (to give the canbody its final profile and shape). A single control system, equipped with a touchscreen panel, permits central operation and control of the entire production line.
2- Piece CAN Production
We build and install complete production lines for deep-drawn round, conical, rectangular or irregularly shaped canbodies. The process usually comprises the following stages: stamping, pre-drawing, final-drawing, embossing, paneling and trimming. Finished cans are then ejected onto an outfeed conveyor that transports them to a packaging table or palletizer.
Deep-drawing systems are designed and manufactured at our Swiss plant in Bergdietikon.
Peel – Off Solutions
compeel technology has made peel-off ends an even more attractive and consumer-friendly alternative to conventional can ends. We developed our modern peel-off technologies because they provide two- and three-piece canmakers with a flexible, convenient and extremely economical solution and enable them to react quickly to changing market needs. UNISEAL endmaking machines integrate easily into existing end production lines and can be used on existing seamers.
Our peel-off ends consist of an aluminum or composite membrane that is attached to a curled ring using tried-and-tested heat-sealing technology on UNISEAL HSS automatic thermo-sealing machines. The machines permit the rapid changeover of end diameters as well as easy operation and maintenance.
END Making
Raw materials account for two-thirds of can costs, and the most effective way to reduce them is to cut material consumption significantly. The easiest way to do so is to downgauge the tinplate used for ends and decrease the cut edge diameter of ends by using mini-seams for thin, hard materials. At the same time, it is vital to ensure that the necessary can resistance values (buckle resistance, panel distension, pullback vacuum value) are retained.
Employing the right end design (developed by FEA) and processing with a multi-stage or thermo-form tooling system offers several advantages. It keeps the end resistance values constant but reduces material thickness and increases the end resistance values using the same amount of material. It reduces thinning of the material, especially in the countersink radius, and also cuts tin and lacquer damage in countersink and panel beads. Furthermore, it keeps the countersink depth constant even at fluctuating temperatures, a factor that is extremely important for EOE shells. Finally, and thanks to a special Cantec seam, it reduces conversion of the seaming machines for seaming DR material ends to a minimum for canmakers and fillers.
Cantec manufactures systems for the high- and medium-speed production of twist-off* caps and PT-caps with guaranteed quality..
Industrial Solutions
Sabatier designs and manufactures custom-made machines for special needs and unique requirements.
The list of special machines and tools developed by Sabatier for individual customer needs is almost endless. It includes automatic dispenser units, tactile marking units and atmospheric closing machines designed for the final closing of rectangular cans for fish, meat and processed food. Our engineers and packaging specialists have unmatched expertise in developing sound solutions for new metal packaging challenges.